اتصل
هاتف
+0086-371-86162511
عنوان
تشنغتشو ، الصين
atmosphere control cement making plant ball mill

Ventilation Prediction for an Industrial Cement Raw Ball Mill by
One of the most critical variables in the cement ball mills is ventilation. A mixture of hot and recycled air would deliver and dry the powder in a cement ball mill as 2021, 14, 3220. https://doi/. 10.3390/ma14123220. Abstract: In cement mills, ventilation is a critical key for maintaining temperature and material transportation. Ventilation Prediction for an Industrial Cement Raw Ball Mill by
احصل على السعر
(PDF) Predictive Controller Design for a Cement Ball Mill Grinding
This paper addresses the design of predictive controller for the cement grinding process using the state-space model and the implementation of this industrially In cement mills, ventilation is a critical key for maintaining temperature and material transportation. However, relationships between operational variables and ventilation factors for an industrial cement ball Ventilation Prediction for an Industrial Cement Raw
احصل على السعر
(PDF) Dust Emission Monitoring in Cement Plant Mills: A Case
Distribution of dust emissions at bag filters in the cement mill section no.1 (mill filterpoint A and separator filter-point B, Figure 1) of the analyzed cement plant.The ultimate ball mill with flexibility built in. You can’t optimise cement grinding with a one-size-fits-all solution. That’s why our ball mills are designed to adapt to your requirements, with a high degree of flexibility built in. You decide whether to operate the mill in open or closed circuit, with or without a pre-grinder and withBall mill for cement grinding FLSmidth
احصل على السعر
Cement plant GAS ANALYSERS FOR BURNER CONTROL, FLUE
ball mill, these become a fine powder that is mixed with gypsum to become cement. Cement particles are so fine that they can flow through a sieve that would retain water. Measurement of pulverized coal, crushed rock and cement dust are equally as important as monitoring of greenhouse gases and chemical pollutants in cement making. Flue gasThe annual cement consumption in the world is around 1.7 billion tonnes and is increasing by 1% every year [].Cement industries consume 5% of the total industrial energy utilised in the world [].A total of 40% of the total energy consumption of a cement plant is used in clinker grinding in a ball mill to produce the final cement product [].Predictive Controller Design for a Cement Ball Mill Grinding
احصل على السعر
Ball Mill Operation -Grinding Circuit Startup & Shutdown Procedure
Normal Shutdown Sequence of Ball Mill and Grinding Circuit. Shut off cyanide metering pump. Put weight controller into MANUAL mode and turn controller output to 0%. Run the ball mill for 15-30 minutes. Put density controller into MANUAL mode, set output to 0%. Put flow controller into MANUAL mode and set output to 0%.The average annual concentration achieved (mg/Nm 3) in 2019 for dust emissions into the atmosphere was approximately ~10% of the maximum limit of the operating license (of 30 mg/Nm 3), that is 3.35 mg/Nm 3, at the emission point FS64 the bag filter of the cement mill, and 3.41 mg/Nm 3 at FS7-21 the bag filter of the cement mill Dust Emission Monitoring in Cement Plant Mills: A Case Study in
احصل على السعر
Ball Mill an overview ScienceDirect Topics
Generally, filling the mill by balls must not exceed 30%–35% of its volume. The productivity of ball mills depends on the drum diameter and the relation of ∫ drum diameter and length. The optimum ratio between length L and diameter D, L: A ball mill, a type of grinder, is a cylindrical device used in grinding (or mixing) materials like ores, chemicals, ceramic raw materials and paints. Ball mills rotate around a horizontal axis, partially filled with the material to be ground plus the grinding medium. Different materials are used as media, including ceramic balls, flint pebblesBall mill
احصل على السعر
Predictive Controller Design for a Cement Ball Mill Grinding
The annual cement consumption in the world is around 1.7 billion tonnes and is increasing by 1% every year [].Cement industries consume 5% of the total industrial energy utilised in the world [].A total of 40% of the total energy consumption of a cement plant is used in clinker grinding in a ball mill to produce the final cement product [].There’s never been a more important time to build resilience into the core of the cement value chain: the cement plant. The cement industry is being hit hard by the COVID-19 pandemic, with global demand for cement expected to decline by 7 to 8 percent in 2020—though these declines have been unevenly distributed across regions. 1 Paul Digitization and the future of the cement plant McKinsey
احصل على السعر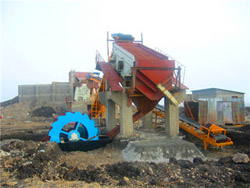
Cement Manufacturing Process and Its Environmental Impact
The cement manufacturing process involves the extraction and processing of raw materials, such as limestone, clay, and shale, which are then heated in a kiln at high temperatures to form clinkerHigh-quality equipment and efficient service make AGICO a trustworthy partner for you! Ball mill is the cement crushing equipment in the cement plant. Compared with open- circuit ball mill, the closed-circuit ball mill has high efficiency, high output, low cement temperature, and good comprehensive benefit. It is the best choice for a cement plant.Ball Mill In Cement Plant Cement Ball Mill AGICO Cement
احصل على السعر
Mill control using millScan g4 Indian Cement Review
This new technology is mill control using vibration sensors, analog to digital converters and digital signal processing (DSP) techniques. It will be shown that significant improvements in material throughput, reduced kilo-watt per tonne numbers, improved material quality can all be realised with vibration control.There are four stages in the manufacture of portland cement: (1) crushing and grinding the raw materials, (2) blending the materials in the correct proportions, (3) burning the prepared mix in a kiln, and (4) grinding the burned product, known as “ clinker ,” together with some 5 percent of gypsum (to control the time of set of the cement).Cement Extraction, Processing, Manufacturing Britannica
احصل على السعر
Cement plant GAS ANALYSERS FOR BURNER CONTROL, FLUE
ball mill, these become a fine powder that is mixed with gypsum to become cement. Cement particles are so fine that they can flow through a sieve that would retain water. Measurement of pulverized coal, crushed rock and cement dust are equally as important as monitoring of greenhouse gases and chemical pollutants in cement making. Flue gasBall mill with Central Drive Mill length Mil l diame te r M il l di amet er 5 3 2 3 2 1 3 5 6 6 4 4 Ball mill with Sid e Driv 1 Inlet 2 Outlet casing 3 Slide shoe bearing 4 Main gearbox 5 Mill motor 6 Auxiliary drive 1 3 Ball mill for cement grinding 3 Cement grinding taking on the tough tasks Cement ball mills have to achieve the desiredBall mill Superior cement quality, More fl exibility, higher
احصل على السعر
(PDF) Predictive Controller Design for a Cement Ball Mill Grinding
The control law obtained in Equation (15) is introduced into the cement ball mill grinding process to optimise the plant for the desired product quality and productivity under larger variations in theoperation of a cement mill, directly extracted from the plant database. In each extraction two days worth of data are loaded, with a sampling period of one minute. Then the software checks for feeder stop-pages and finds continuous operational data sets of 250 minutes duration. In parallel it detects the ce-== s, A (m)OPTIMIZING THE CONTROL SYSTEM OF CEMENT MILLING:
احصل على السعر- مصنع تلبيس خام الذهب الفك
- معدات التعدين المستوردة إلى الصين
- omann تهتز الموردين الشاشة
- amanama gold mining company
- الکتریکی سیم پیچ ویبراتور
- معدن سنگ دستگاه شکستن
- فروشگاه سنگ شکن
- grinder price mi er
- تأجير محطم ملموسة في نيويورك
- مطحنة خام الذهب القرص مرشح
- كسارة الصخور كانيون بافيليون كسارة الصخور Rd نهر الكريستال فلوريدا
- portable limestone cone crusher provider south africa
- أسعار الصخور المسحوقة في محطم الهند المحجر
- الفك محطم اليابان للبيع
- صور نماذج كسارة المطرقة