اتصل
هاتف
+0086-371-86162511
عنوان
تشنغتشو ، الصين
Calculate Media Charge In A Ball Mill
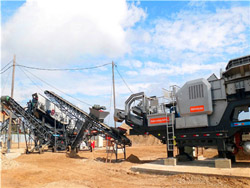
Mill Steel Charge Volume Calculation 911 Metallurgist
We can calculate the steel charge volume of a ball or rod mill and express it as the % of the volume within the liners that is filled The ball charge is determined by the operator targeting the balance between grind and throughput, the higher the ball charge the more aggressive the milling becomes. With Ball Mill Charge Grinding & Classification Circuits Metallurgist
احصل على السعر
ball mill charge volume calculation marketreachcalculator
Ball mill charge volume calculation can be used to determine the optimal operating conditions for the mill, such as the optimal charge volume, speed, and where: db max is the maximum ball diameter in a charge, d is the characteristic top limit of the material size which is being ground (d95 or d80 in the formulae is recommended for THE OPTIMAL BALL DIAMETER IN A MILL 911 Metallurgist
احصل على السعر
Simulation of charge motion in ball mills. Part 1: experimental
Herein, an innovative approach for determining the grinding media system of ball mill based on grinding kinetics and linear superposition principle was proposed. The combination of a grinding circuit simulator with a model of ball wear in a grinding mill leads to a method to calculate, with a preselected accuracy, the make-up ball charge that...Optimization of the make-up ball charge in a grinding
احصل على السعر
Simulation of charge motion in ball mills. Part 2: numerical
Herein, an innovative approach for determining the grinding media system of ball mill based on grinding kinetics and linear superposition principle was proposed. Abstract and Figures. The paper presents an overview of the current methodology and practice in modeling and control of the grinding process in industrial ball mills. Basic kinetic and energy(PDF) Grinding in Ball Mills: Modeling and Process Control
احصل على السعر
(PDF) Grinding in Ball Mills: Modeling and Process
A ball mill is a type of grinder widely utilized in the process of mechanochemical catalytic degradation. It consists of one or more rotating cylinders partially filled with grinding balls (madeAbstract and Figures. The combination of a grinding circuit simulator with a model of ball wear in a grinding mill leads to a method to calculate, with a preselected accuracy, the make-up ballOptimization of the make-up ball charge in a
احصل على السعر
Ball Mill Parameter Selection & Calculation JXSC
Critical Speed_. When the ball mill cylinder is rotated, there is no relative slip between the grinding medium and the cylinder wall, and it just starts to run in a state of rotation with the cylinder of the mill. This instantaneous speed of the mill is as follows: N0 —- mill working speed, r/min; K’b — speed ratio, %.2.4 Effect of ball size 29 2.4.1 Empirical approaches 29 2.4.2 Probabilistic approaches 33 2.5 Abnormal breakage 36 2.6 Effect of ball mixture 37 2.6.1 Ball size distribution in tumbling mills 37 2.6.2 Milling performance of a ball size distribution 40 2.7 Summary 41 Chapter 3 Experimental equipment and programme 43EFFECT OF BALL SIZE DISTRIBUTION ON MILLING PARAMETERS
احصل على السعر
Power Draw of Grinding Mills its Measurement and Prediction
Among the most important models developed, we can refer to the models related to different types of ball mills (Bond, 1952;Lynch, 1977), Autogenous (AG) and Semi autogenous (SAG) mills (LeungGenerally, filling the mill by balls must not exceed 30%–35% of its volume. The productivity of ball mills depends on the drum diameter and the relation of ∫ drum diameter and length. The optimum ratio between length L and diameter D, L: Ball Mill an overview ScienceDirect Topics
احصل على السعر
Study on heat transfer behavior and thermal breakage characteristic of
Ball mill is an energy-intensive device for grinding and breaking iron ore particles, which is extensively used in mineral, cement, chemical, and other industries. 1–4 In the field of mineral processing, a portion of the energy is converted into heat that will raise the milling temperature and breakage characteristics of iron ore will be changed Predicting charge motion, power draw, segregation and wear in ball mills using discrete element methods. Miner. Eng. (1998) An innovative approach for determining the grinding media system of ball mill based on grinding kinetics and linear superposition principle. Powder Technology, Volume 378, Part A, 2021, pp. 172-181.Impact energy of particles in ball mills based on DEM simulations
احصل على السعر
Impact Load Behavior between Different Charge and Lifter in a
1. Introduction. A ball mill (Figure 1) is the key piece of equipment for secondary grinding after crushing and is suitable for grinding all types of ores and other materials.Ball mill are used in the mining, cement, chemical and agricultural industries, particularly tumbling ball mills [1,2,3,4].The comminution process is dependent on the Due to the complexity of charge motion inside a ball mill, it is very difficult to calculate some mean shear rate accurately. Klimpel (1984) estimated the shear rates to range from 0 to 60 s −1, but no evidence was given as to how this figure was calculated. Mishra (1991) and Mishra and Rajamani, 1994a, Mishra and Rajamani, 1994b used theEstimation of shear rates inside a ball mill ScienceDirect
احصل على السعر
A population balance model of ball wear in grinding mills: An
Section snippets Materials and methods. The experimental work was performed by using a laboratory mill of diameter 570 mm and length 220 mm.The mill was filled with 54.84 kg of alumina balls of three different sizes (40.5 mm, 30.7 mm, and 26.9 mm) with a fill factor J = 45 %, and operating at 75% critical speed.A uniform ball size Overcharging results in poor grinding and losses due to abrasion of rods and liners. Undercharging also promotes more abrasion of the rods. The height (or depth) of charge is measured in the same manner as for ball mill. The size of feed particles to a rod mill is coarser than for a ball mill. The usual feed size ranges from 6 to 25 mm.Mill Charge an overview ScienceDirect Topics
احصل على السعر
Ball Charge in Ball Mill PDF Mill (Grinding) Energy And
Todays ball mills are typically designed to operate with ball charge fillings up to 35% by volume. There are cases where this figure is higher, for example with mill shells designed for higher loadings, but these cases are becoming more rare, with the additional cost of steel becoming prohibitory of this design.However, almost all of the classical theories for calculating the power consumption of ball mills disregard the effect of lifters and only focus on rotation rate, charge fill level, as well as size and shape of grinding media, thereby may causing errors. Discrete element method (DEM) can simulate the motion and interaction of particle A method to predict shape and trajectory of charge in industrial mills
احصل على السعر
Ball Mill Design/Power Calculation 911 Metallurgist
Mill type. These conditions have been built into factors which are given in the figure above. The approximate horsepower HP of a mill can be calculated from the following equation: HP = (W) (C) (Sin a) (2π) (N)/ 33000. where: W = weight of charge. C = distance of centre of gravity or charge from centre of mill in feet.Microsoft Word info_ball_mills_ball_charge_en.docx Author: ct Created Date: 4/4/2019 9:22:48 AMBall and Jar Guide Cole-Parmer
احصل على السعر
Calculation of energy required for grinding in a ball mill
INTRODUCTION The energy consumption for grinding, according to Bond (1961), is deter- mined by the formula: / 10 10 (I) The work index is determined by grinding experiments carried out in a labo- ratory Bond ball mill. Based on the results of grinding experiments, numerical values of the work index Wi are calculated according to the planetary ball mill that is different from tumbling mills in many aspects. Djordjevic (2005) studied the. influence of ball charge size distribution on the net-power draw of tumbling mill by DEM(PDF) Effects of Ball Size Distribution and Mill Speed and Their
احصل على السعر
Effect of lifters and mill speed on particle behaviour, torque, and
The net power draw and media charge position were measured. After this, the slurried ore was gradually added to the media charge for slurry filling U between 0 and 3. A proximity probe and a conductivity sensor mounted on the mill shell provided a means of measuring both the position of the media charge and that of slurry.Measuring filling is also necessary to estimate the composition of the load for mill modelling: rock and slurry for AG mills; rock, balls and slurry for SAG mills; or balls and slurry for ball mills. In the case of SAG mills, this requires two separate filling measurements: one for a crash-stop and one following a complete grind-out to quantify An improved method for grinding mill filling ScienceDirect
احصل على السعر- محطه غسل الرمالكسارة الأحجارمعدات لتكسير
- الطاحن مصنعين مطحنة
- طاحونة الرول العمودية
- mini crusher for sale kenya
- ففد على كسارة الفك
- عملية مخطط تدفق نظام محطم الفحم
- طاحونة الفرق الفرق
- crushed fine aggregate for gardens pathways
- غبار آلة تكسير الحجارة في الهند
- كسارة لعملية تصنيع الرمال الصخرية
- سعر مصنع كسارة الصخور في الهند
- washing equipment for molybdenum ore in the asia pacific region
- تطبيق الكلي الكسارات قوات الدفاع الشعبي
- كسارة لفة محمولة للشراء في السعودية
- القدرة محطم للبيع