اتصل
هاتف
+0086-371-86162511
عنوان
تشنغتشو ، الصين
iron ore grinding mill parts

Research of iron ore grinding in a vertical-roller-mill
Holger Lieberwirth a Add to Mendeley https://doi/10.1016/j.mineng.2014.07.021 Get rights and content • Two magnetite iron The application of vertical mills in regrind circuits is consolidated. This type of mill is now attracting interest in primary grinding applications, due to its higher Vertical mill simulation applied to iron ores ScienceDirect
احصل على السعر
Investigation on Iron Ore Grinding based on Particle Size Distribution
The new approach is adapted to identify the retention time (RT) of the iron ore in the mill, and the total RT taken for the blend sample in the Bond’s ball mill is The grinding parts of a Loesche mill (Fig. 1) are a rotating table (1) with a horizontal grinding track and rollers (2), which are pressed onto the table by lever arms Research of iron ore grinding in a vertical-roller-mill
احصل على السعر
Stirred Mill SpringerLink
With the advantages of high grinding efficiency and less area occupation, it is widely used in the regrinding, fine grinding, and ultrafine grinding process of such Evaluation of grinding circuits for iron ore March 2019 Authors: Marly Carvalho University of Oulu Carlos Pereira Francielle Câmara Nogueira Abstract and (PDF) Evaluation of grinding circuits for iron ore
احصل على السعر
Mechanism of magnetite iron ore concentrate morphology
Ball milling (BM) and High-pressure grinding rolls (HPGR) are commonly employed for grinding iron ore concentrate [18], [19], [20]. In BM, the particle size was Modern iron ore pelletizing process operations may be divided into two main process sections: feedstock preparation and agglomeration processes. In most Development of a Novel Grinding Process to Iron Ore
احصل على السعر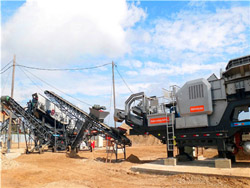
(PDF) Physicochemical Problems of Mineral
An effect of a grinding method, that is ball mill and high pressure grinding rolls (HPGR), on the particle size, specific surface area and particle shape of an iron ore concentrate was studied.Abstract. The application of vertical mills in regrind circuits is consolidated. This type of mill is now attracting interest in primary grinding applications, due to its higher efficiency when compared to ball mills, which are usually used at this stage. In this study, a coarse sample of iron ore was tested in a pilot scale grinding circuitVertical mill simulation applied to iron ores ScienceDirect
احصل على السعر
Mill shell. Mill head bolts.building material. Grinding mills spare parts TON These include: trunnion seals,lube pumps,filters,and seals.We can accelerate our production of custom made grinding mill parts,such as shells,trunnions,trunnion seals and liners and mill heads. Analysis of the criticality of flaws found in trunnion of.Improvement of concentrate quality by using fine screening in iron ore grinding stages. 2023, Chernye Metally Studying the integration of solar energy into the operation of a semi-autogenous grinding mill. Part I: Framework, model development and effect of solar irradiance forecasting. Minerals Engineering, Volume 137, 2019, pp. 68-77.TowerMill circuit performance in the magnetite grinding
احصل على السعر
Feed hardness and acoustic emissions of autogenous/semi
In this study, the relationship between acoustic emissions and hardness of different rock types (model quartz, model calcite, and real iron ore) coupled with binary mix ratios of model quartz and iron ore (1:3, 1:1 and 3:1) was investigated in a laboratory-based AG/SAG mill. The acoustic emission response and sensitivity of the mill wereThere are several pre-concentration technologies available, one of them being ore sorting (Cutmore et al., 1998, Iyakwari and Glass, 2014, Lessard et al., 2014, Lessard et al., 2015, Robben and Wotruba, 2019).Adoption of sensor-based ore sorting solutions that reduce energy consumption and rationalise water use is becoming of more Towards waterless operations from mine to mill ScienceDirect
احصل على السعر
(PDF) Process Mineralogical Assessment of the Grinding
Currently, the high-grade iron ore deposit of Kiirunavaara has a low grade of silica in situ, of approximately 3.0% SiO 2,but the silica grade is expected to increase in the deeper parts of thePeng Y X, Li T Q, Zhu Z C, et al. Discrete element method simulations of load behavior with mono-sized iron ore particles in a ball mill. Adv Mech Eng, 2017, 9(5): 1 [23] Kalala J T, Breetzke M, Moys M H. Study of the influence of 离散元法在磨矿设备及参数优化研究中的应用现状 USTB
احصل على السعر
High-Pressure Grinding Roller Presses for Minerals
Redevelopment of the large mill line 2012 Introduction of HYBRIDUR® wear protection with studded linings Improved design: MHF Multi-Hinged Frame 2013 First HPGR delivered for iron ore pellet feed 2014 New HPGR machine sizes introduced ranging from 1.0m to 2.54m roller diameter 2018 More than 880 roller presses supplied to 68 Much of the remaining iron ore resources in Brazil consist of low-grade itabirite ores. Accordingly, a typical beneficiation circuit includes a four-staged crushing/screening plant, followed by grinding in a closed-circuit ball mill, desliming in hydrocyclones and final ore mineral concentration via multistage reverse flotation and Transforming iron ore processing ScienceDirect
احصل على السعر
Developments in iron ore comminution and classification
The Zourerat iron ore mine has two 1.7 m diameter × 1.8 m wide HPGR units treating 1400 t/h each of aerofall mill pebbles. The feed is − 25 + 1.6 mm and has a ball mill work index of 12–14 kWh/t. The iron ore has low to moderate abrasion characteristics. Figure 8.21 shows the Zourerat iron ore flowsheet.For example, Katircioglu-Bayel et al. (2019) explored the influence of grinding media filling level on energy consumption and ore crushing in a stirred media mill through experiment.Influence of Grinding and Classification Circuit on the
احصل على السعر
Iron ore crushing and screening process TY Ultrafine
The iron ore processing and production process mainly includes three processes: crushing, grinding and beneficiation. In the crushing process, the three-stage closed-circuit crushing is more modern and suitable for high-hardness iron ore crushing and can complete the work of ore crushing and partial dissociation, thereby improving the The developed device and ball mill were used separately for the grinding of prepared copper ore feeds. It was reported that 66% energy was saved when compared with the ball mill. A similar idea was developed called the Ultrasonic High-Pressure Roller Press (UHPRP), which was used in the investigation of the grinding characteristic of copper oreMethods of Ore Pretreatment for Comminution Energy
احصل على السعر
Special Issue "Grinding Modeling and Energy Efficiency in Ore
The results show that grinding time is a significant factor affecting the particle size composition. The suitable grinding concentration of Tongkeng ore and Gaofeng ore is 70% and 75%, respectively. The effect of mill filling ratio on Gaofeng ore is not obvious. The rotational rate has little effect on the grinding technical efficiency.Nowadays, the HPGR (high-pressure grinding rolls) is an intermediate step between filtering and balling in the most modern iron ore pelletizing operation.(PDF) Iron Ore Concentrate Particle Size Controlling Through
احصل على السعر
Iron ore grindability improvement by microwave pre-treatment
The modification of magnetic properties of siderite ore by microwave energy resulted in increasing the efficiency of their magnetic separation. Pre-treatment in a microwave oven with maximum power of 900 W of weakly paramagnetic ore (25.1% Fe, 9.6% SiO 2) was realized with the samples (100 g) of iron spathic ore of particle size Grinding iron ores in conventional ball mills involve a considerably high consumption of metallic media, resulting in high operating costs. In the case of compact itabirites, the high silica content increases such consumption, potentially exceeding the costs associated with electric power consumption in industrial operations. This paper presents Study on Partial Replacement of Metal Grinding Ball with
احصل على السعر
Iron Ore Concentrate Particle Size Controlling Through
Nowadays, the HPGR (high-pressure grinding rolls) is an intermediate step between filtering and balling in the most modern iron ore pelletizing operation. The operation debottlenecks filtering process and reduces pressure over the typical milling process to control particle size to the balling. The present study evaluated aspects of microwave The iron ore pellet market is expected to achieve stable growth from 2021 to 2028. According to the analysis of Data Bridge Market Research, the market is growing at a CAGR of 3.6%. The iron ore pellet market is mainly driven by the growing need for steel in end-use industries such as the automobile industry, shipbuilding industry, constructionIron Ore Pelletizing Plant Iron Ore Pelletizing Pellet Plant
احصل على السعر
The performance improvement of a full-scale autogenous mill by setting
From the stockpiles, the ore is conveyed to the primary grinding circuit (Fig. 1). As can be seen, the primary grinding circuit comprises an AG mill, 9.76 m diameter by 4.27 m length (throughput = 650 t/h), in closed circuit with scalper and banana screens. The. The effect of direct addition large lumps of ore to the AG mill on its performance
احصل على السعر- كسارة Pex 150 X
- معدات التنقيب عن الماس في جنوب أفريقيا
- المحمول محطم خام الحديد للبيع أنغولا
- how to setup a cement block industry in nigeria feasibility
- نظام سحق الهيدروليكي
- سعر معدات التعدين المستعملة في السعودية
- مطحنة من الأحدث
- Tromill For Alluvial Mining
- تقسيم الحجر الهيدروليكي آلة كسارة مخروطية هيدروليكية
- كم تكلفة معدات كسارة الذهب
- انواع ماشین سنگ خرد کن
- iron ore pellet plant technology
- مصنع صنع مسحوق الجبس المحمولة
- كسارات للإيجار بالقرب من وينكانتون
- نوع جديد من خامات الذهب للبيع في أستراليا