اتصل
هاتف
+0086-371-86162511
عنوان
تشنغتشو ، الصين
cement mill of cement plant

Digitization and the future of the cement plant McKinsey
Our vision: The leading cement plant of 2030. The cement plant of the future achieves considerably lower operating costs and higher asset value through higher energy efficiency, yield, and throughput. More targeted and effective maintenance In general, cement mill can both apply for dry cement production and wet cement production. Commonly, there are three hot types of cement mill in the cement industry: cement ball mill, Raymond mill, and vertical cement Cement Mill Cement Ball Mill Vertical Cement
احصل على السعر
Optimization of Cement Manufacturing Process ScienceDirect
Optimization of Cement Manufacturing Process. Cement manufacturing process is now operated with the aid of various control systems, such as raw meal Cement production is one of the most energy-intensive manufacturing industries, and the milling circuit of cement plants consumes around 4% of a year's Modeling of energy consumption factors for an industrial cement
احصل على السعر
Energy and exergy analyses for a cement ball mill of a new
Nowadays, ball mills are used widely in cement plants to grind clinker and gypsum to produce cement. In this work, the energy and exergy analyses of a cement Nowadays, ball mills are used widely in cement plants to grind clinker and gypsum to produce cement. In this work, the energy and exergy analyses of a cement Energy and exergy analyses for a cement ball mill of a new
احصل على السعر
The cement mill Understanding Cement
Cement clinker is usually ground using a ball mill. This is essentially a large rotating drum containing grinding media normally steel balls. As the drum rotates, the motion of the balls crushes the clinker. The drum rotates PDF On May 13, 2021, Elshan Moradkhani and others published Intelligent Modeling of Cement Plant Mill Unit Using Artificial Neural Networks and Real Data Find, read and (PDF) Intelligent Modeling of Cement Plant Mill Unit Using
احصل على السعر
What are the parts of a mill in a cement plant? LinkedIn
A cement mill is an important component of the cement manufacturing process in a cement plant. It is responsible for grinding clinker, gypsum, and other A cement ball mill is ready for transportation. There are many kinds of industrial equipment used in a cement plant, including thermal equipment, grinding equipment, dust removal system, transportation system, storage system, and so on.When placing an order, we may need to order different equipment from multiple manufacturers at the same time.How to Start a Cement Factory Design & Construction of Cement Plants
احصل على السعر
Cement Plant an overview ScienceDirect Topics
The Ramla cement plant (see Fig. 1 for an aerial photo of the plant) has been in operation for 46 years. The original process at the Ramla cement plant to produce cement from limestone, which is the base material of cement, was a so-called wet line process. The original wet line had a capacity of 1,800 TPD (Tons Per Day).AGICO Cement is a cement equipment manufacturer with more than 20 years’ experience. We are the long-term partner of many large and medium-sized cement enterprises in different countries, providing cement Ball Mill In Cement Plant Cement Ball Mill
احصل على السعر
Modeling of energy consumption factors for an industrial cement
Database. The provided data were collected from a cement plant (Fig. 1) located in Ilam, west of Iran.The plant has two cement production lines which in total produces 5300 t/day cement.Nowadays, ball mills are used widely in cement plants to grind clinker and gypsum to produce cement. In this work, the energy and exergy analyses of a cement ball mill (CBM) were performed and some measurements were carried out in an existing CBM in a cement plant to improve the efficiency of the grinding process. The first and second Energy and exergy analyses for a cement ball mill of a new
احصل على السعر
Technological Energy Efficiency Improvements in Cement Industries
The cement industry is highly energy-intensive, consuming approximately 7% of global industrial energy consumption each year. Improving production technology is a good strategy to reduce the energy needs of a cement plant. The market offers a wide variety of alternative solutions; besides, the literature already provides reviews of Steel balls are one of the most widely used grinding media in cement ball mills, their diameters can range from 20mm to 120mm according to different grinding requirements. In a cement ball mill, generally, φ50–100mm steel balls are used in the coarse grinding chamber, φ20–50mm steel balls are used in the fine grinding chamber. 2.How to choose proper grinding media for your ball mill
احصل على السعر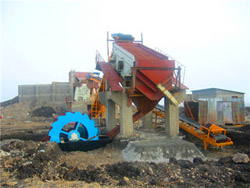
Optimization of Cement Manufacturing Process ScienceDirect
Ball mill control -Automatic start-up control In most cement plants, start up of a mill is conducted through a series of manual operations on the part of an operator. The operator switches on the mill, starts the mill feed and,after ascertaining that the mill load becomes stable,changes the control mode to the constant-value feedbackNowadays, ball mills are used widely in cement plants to grind clinker and gypsum to produce cement. In this work, the energy and exergy analyses of a cement ball mill (CBM) were performed andEnergy and exergy analyses for a cement ball mill of a new
احصل على السعر
Cement Plant Cement Manufacturing Plant EPC Project
The cement manufacturing plant can be divided into five steps: Crushing & prehomogenization: cement crusher crush limestone and other materials and stacker and reclaimer homogenize them. Raw material preparation: use cement mill to process materials into required sizes for cement clinker production. Clinker production: In the cyclone Empirical study of a type of cement plant. The LN cement plant, located in the south-west of Shandong Province, was considered as a case study for the mass flow and balance analysis. This cement plant operates on a dry process line with a five-stage suspension pre-heater and an inline pre-calciner. The kiln is 4 m in diameter and 60 m in Analysis of material flow and consumption in cement
احصل على السعر
How many cement plants are producing in the
Cemex own a total of 61 plants; 52 active integrated plants and nine active grinding plants which yields a total of 91.6Mt/yr of cement capacity. It operates 13 plants and 46 cement terminal in the united Cement manufacturing is the source of 5% of global CO2 emissions. 60% of emissions are due to the transformation of raw materials at high temperatures and 40% results from the combustion required to heat the cement kilns to 1500°C. Therefore emissions monitoring is extremely critical for cement plants to meet regulatory requirements.Cement Analysis and Production Information Thermo
احصل على السعر
(PDF) IMPROVING THERMAL AND ELECTRIC ENERGY EFFICIENCY AT CEMENT PLANTS
Improving Thermal and Electric Energy E ciency at Cement Plants: International Best Practice. Grinding Portland cement with a Blaine of 3,200. approximately 23 kWh per ton, and even for pozzolanicHistory. Kawasaki Heavy Industries, Ltd. has supplied a lot of cement manufacturing equipment worldwide since its first delivery of a rotary kiln in 1932. The cement plant we designed and constructed has attracted the attention of the world's cement manufacturers and specialists due to its advanced performance.Cement Plant Kawasaki Heavy Industries
احصل على السعر
Dust Emission Monitoring in Cement Plant Mills: A Case
This paper is a case study of a Portland cement plant in Romania, the experimental determinations presented mainly focusing on dust emissions in an important sector of the plant (cement mill and related facilities), with dust extraction from two chimneys in working areas (cement mill filtration system and grinder component separator filtrationcement ball mill. Application: limestone, clay, coal, feldspar, calcite, talc, iron ore, copper, phosphate, graphite, quartz, slag. Capacity: 0.65-615T/H. The cement ball mill usually can be applied to raw meal grinding or cement grinding. Besides, the cement ball mill also can be used for metallurgical, chemical, electric power, other miningRaw Mill, Cement Raw Mill, Raw Mill In Cement Plant Cement
احصل على السعر
Cement Sumitomo Drive
We offer high-torque cement mill drives that are vital links in the manufacturing process of cement plants worldwide. Large Industrial Gearbox for Mill. Customizable to meet your needs. Torque range. 29000 Nm 4817000 Nm. 256671 in-lbs 42634000 in-lbs. Ratio range. 20:1 68:1. 20:1 68:1.β [1 − α; p 2; n − p − 1 2] = (1–α) th quantile of β [p 2; n − p − 1 2] distribution. For α = 0.05, the number of outliers is 44 among 280 data corresponding to an upper limit control U C L M a h a l a n o b i s = 4.55 as illustrated in Fig. 3.The results of these outliers have been carefully analyzed by a process expert from the cement plant. Efficient machine learning model to predict fineness, in a
احصل على السعر
Load-shifting opportunities for typical cement plants SciELO
Load-shifting opportunities can be found in the layout of the plant and the flow rates of the equipment. The flow rates of the raw mills, cement mills and kilns can be seen in Figure 2. These were determined by averaging a daily record of the equipment performance over a period of three months, 1 May to 31 July 2010.
احصل على السعر- كسارات مخروطية تركيا
- hard rock gold mining techniques
- مصنع تكسير وغربلة كامل للركام
- معدات تجهيز خام الكبريت
- سعر كسارة فكية 200 pe900
- crusher 300 ton per hour second hand for sale india
- آلة التعدين Gwm سوبر مايكرو مطحنة
- آلات الحفر محيط سياج
- آلة كسارة الحجر tph مصر
- texnologicheskogo processa trub metallurgicheskogo kombinata
- كسارة الفحم في ص
- مقدمة من وحدة تكسير الحجارة لتقرير المشروع في الهند
- آلة تكسير الدولوميت في الجزائر
- canada centrifugal slurry pump bomba parts factory
- هزینه های سنگ شکن های بتنی